
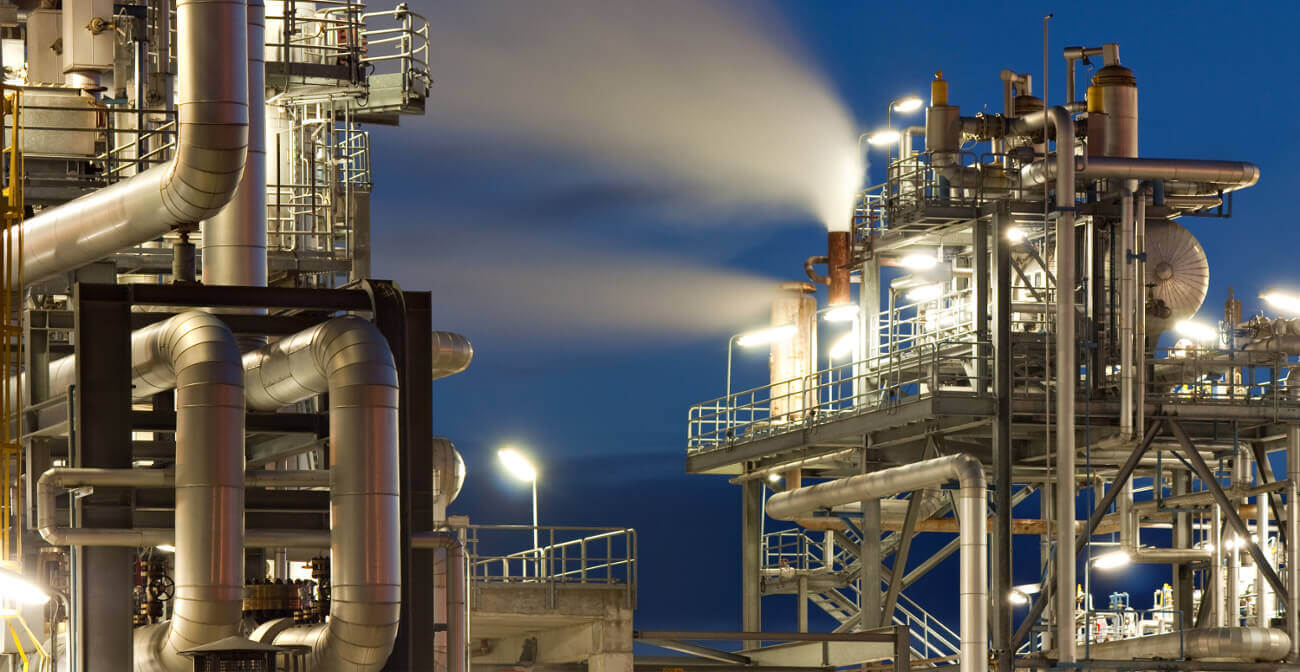
Heat exchangers in petrochemicals
The heat exchangers used in various steps in the processing of oil and natural gas are subject to severe environmental constraints and high pressures.
They must satisfy demanding reliability requirements because of the types of fluids in them (flammable, explosive, harmful to the environment, etc.). This generally makes it necessary to use ASET tubular exchangers.
Barriquand and ASET heat exchangers in petrochemistry
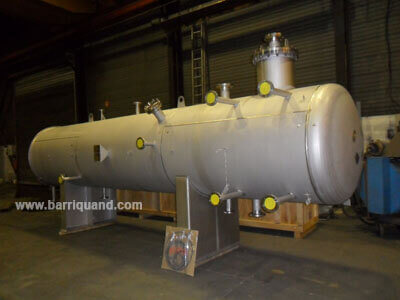
The very broad range of Barriquand plate heat exchangers and shell and tube heat exchangers covers all steps in the processing and transport of the various sources of hydrocarbons (oil, methane, shale gas, etc.).
During refining:
- Evaporator, condenser
- Cooler for gas scrubbing water (quench water coolers)
- Amine recovery on gas cleaning
Before the hydrocarbons are used as sources of energy or as feedstocks:
- Heating of natural gas, before or after expansion (to avoid freezing the ground)
- Heating of fuels (fuel-oil, diesel fuel, crude oil, kerosene, HVF, tar, etc.) in order to lower their viscosity
- Heating of bitumen and coated materials
- Cooling of hydraulic turbine or transformer oil
Particular requirements and technical specifications for each exchanger impose suitable dimensioning and design.
Construction file and quality tracking of the exchangers

Barriquand meets the specific needs of the various players in the sector in the choice of the design, of the various types of construction, and of the grades of materials.
Barriquand builds exchangers compliant with the various codes of construction (CODAP, ASME, etc.) and applicable regulations (PED, U STAMP, SELO, TÜV, etc.).
For each exchanger, the Barriquand and ASET engineering design departments prepare a construction file. Each step in production, up to final receiving in the plant, is validated by the quality departments under the supervision or oversight of approved organizations and designated inspectors.
The strengths of Barriquand exchangers in petrochemicals
Thermal and hydraulic dimensioning:
- Thermal efficiency: high exchange coefficient
- Dimensioning with very low temperature pinches
- Building of high-pressure exchangers – up to 500 bar
- Low losses of head
- Fouling and/or viscous fluids
Construction, design:
- Straight-tube exchanger or U-tube exchanger with free expansion
- Smooth, wide channels, with no points of contact, that can be adapted to the fluids
- Compact
- Self-draining circuit
- Installation in horizontal or vertical position
- Many materials possible
Other heat exchanger applications
- Exchangers on utility fluids
- Exchangers on CIP (cleaning in place)
- Production of hot water
- Fuel heaters (natural gas, heavy fuel oil)
- Kettle (evaporator-condenser, heat transfer oil, superheated water, etc.)